《「見える化」による改善活動》支援
「見える化」は、問題解決の基本です
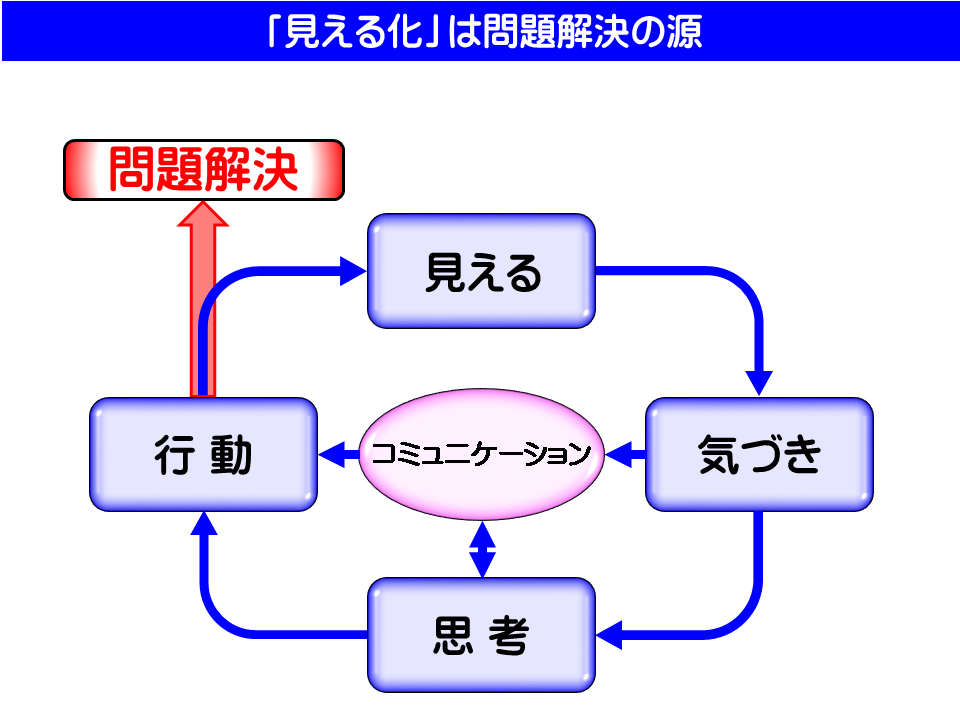
現場ではさまざまな問題が山積していますが、問題の原因を追求する際に、問題を視覚的に「見える」ようにすることが必要不可欠です。
人間は外部からの情報の約80%を視覚から得ると言われています。物事が「見える」ことによって、新たな気づきが生まれ、その気づきによって思考が生まれます。
これにより、さまざまな事象や事実がより明確になり、各自や組織間で共通認識が形成されます。
その結果、各自や組織間の壁が取り除かれ、コミュニケーションが促進されます。「思考」や「コミュニケーション」を通じて、新たな発想や創意工夫が生まれます。
そして、どのような行動を取ればよいのかという仮説を得たら、それを実行したいという欲求が生まれ、「行動」に繋がります。行動すれば必ず結果が生じ、問題が解決されます。
このように、「見える化」によって、「見える化→気づき→思考→コミュニケーション→行動」という連鎖反応が起こり、問題解決が実現されるのです。
見える化のメリット
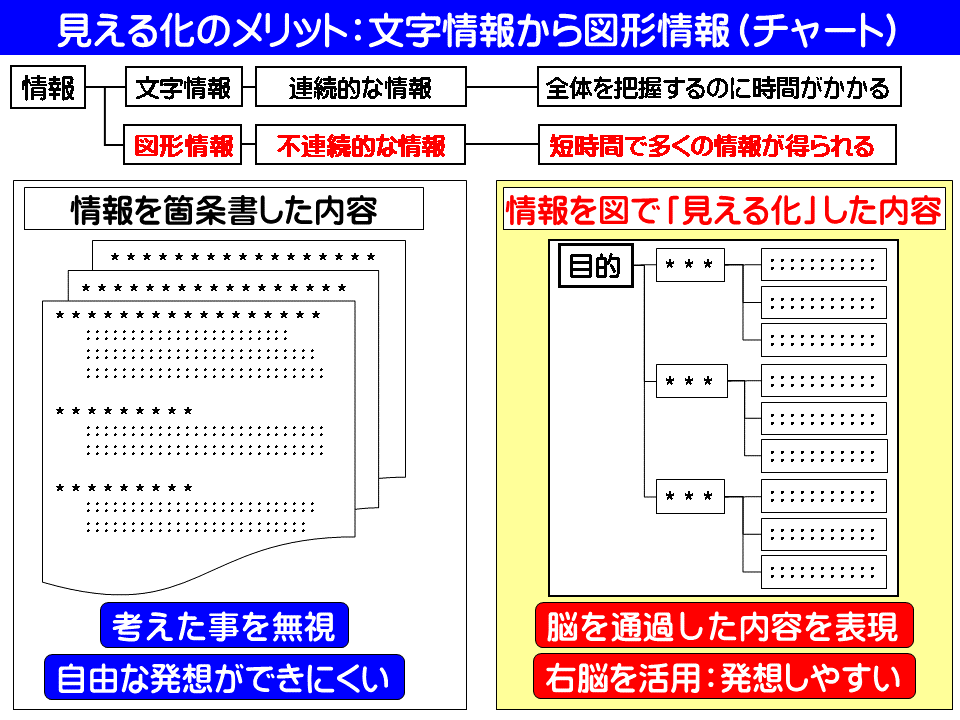
情報を文字情報としてまとめると、連続的な情報として把握するためには時間がかかります。
また、要素や材料間の関係がわかりにくくなります。一方、情報を図解情報として系統図(チャート)にすると、一目で情報の全体像が得られます。
その結果、全体のプロセスや要素の関係を短時間で把握し、各要素や材料の関連性を瞬時に理解できます。
このように情報を図解して「見える化」することで、全体の把握と細部の関連が容易になり、「全体最適」と「部分最適」の達成が可能となります。
見える化の体系化
見える化」を体系化するために、前述のチャートを利用してプロセスの「見える化」を行います。これは全体のプロセスを「見える化」し、関連付けを行い、さらに数値化します。関連付けとは、各プロセス間の関係を図示することです。
数値化とは、各プロセスの工数や材料、パラメーターなどを表現することです。これらを体系化し、それを「TPM(Total Process Management)」と名付けて実践します。
TPMとは
下記の頭文字をとってTPMとしている.
T:Total(総合的、全体的)
P:Process(プロセス)
M:Management(マネジメント)の頭文字を取った言葉です。
TPMは全体を総合的に「鳥瞰」(見える化)し、各プロセスを「紐づけ」(関連付け)して、末端の部品仕様を「数値化」する手法です。TPMの目的は、全体最適と個別最適を実現することです。
「業務TPMチャート」の作り方

「業務M・TPMチャート」は、情報とモノの流れを下記の手順は以下の通りです
- 時間の概念を可視化し、工数は四角(□)で表記します
- 価値のない時間や作業の滞留時間、判断時間などを矢印で示し各プロセス(作業)の所要時間に比例したチャートを作成します
- 縦軸に関係する部署を記載します
このように「モノ」と「情報」の流れを描写すると、問題点が明確になり、クリティカルパスやボトルネックが容易に抽出できます。
商品M・TPMチャート
「商品M・TPM」チャートは、開発・設計のやり方を機能展開によって示し、以下の手順に従います。
(1)最初に商品要求仕様をどのような手段(1次手段)で達成するかを記述します
(2)1次手段を目的としてどのような手段(2次手段)で達成するかを記述します
(3)2次手段を目的としてどのような手段(3次手段)で達成するかを記述します
(4)この機能展開を繰り返します
最終段階で最小単位の部品や材料やパラメータが明確になります
車の機能系統図(参考チャート)
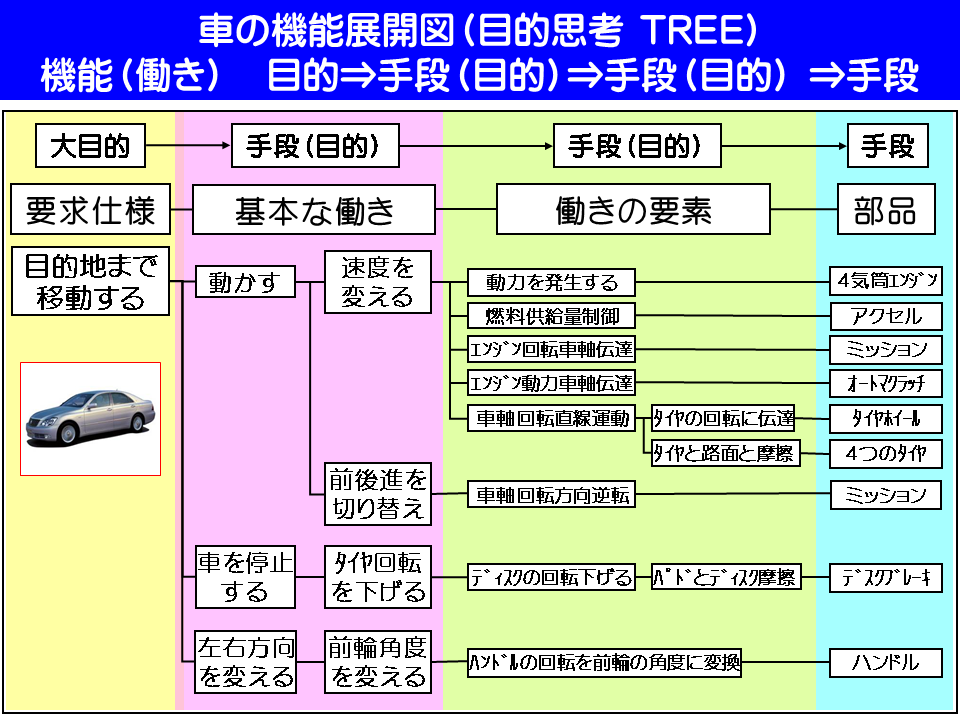
車の機能系統図は下記のように展開します
- 大目的(要求仕様)車の働きを左上に書きます
- 1次手段(基本的な働き)を2段目に書かきます
- 1次手段を目的として2次手段(働きの要素)を書きます
- 2次手段を目的として3次手段(部品)を書きます(エンジン,ブレーキ,ハンドル等)
これにより、車の機能(働き)のメカニズムや部品の働きが、誰が見ても一目で理解できるようになります
以上のように、弊社では人材教育(意識改革)を土台とした「見える化」による「業務改革」を支援しております。これにより、物理的な面と心理的な面の両方から、組織の改善活動を促進しています。
「見える化」による業務改善支援事例:下記をクリック
お気軽にお問い合わせください。092-565-1426受付時間 9:00-18:00 [ 土・日・祝日除く ]
お問い合わせ